Os processos em uma empresa são essenciais para os resultados no longo prazo. Mas, para manter um certo nível de entregas, é necessário investir em metodologias como o ciclo PDCA. Essa abordagem estimula um ciclo de melhorias constantes no dia a dia da operação.
Imagine uma fábrica de bebidas em que cada mililitro fora da especificação vira perda direta de receita. Garantir que esses detalhes sejam colocados em perspectiva para alcançar melhores resultados é essencial e, por isso, adotar o ciclo PDCA pode ser uma alternativa interessante.
Esse método não é novo, mas continua atual porque cria um roteiro simples para testar hipóteses e aprender rápido. Quando bem aplicado, é enorme o potencial desse modelo para quem precisa entregar crescimento sustentável, reduzir riscos e engajar times em diferentes localizações.
Para entender como funciona, como colocá-lo em prática e mais detalhes, preparamos um conteúdo completo. Continue a leitura e confira!
O que é o ciclo PDCA?
O PDCA é um framework iterativo composto por quatro etapas que guiam o aprendizado prático e a padronização de processos. O acrônimo vem de Plan (Planejar), Do (Executar), Check (Verificar) e Act (Agir).
Popularizado por W. Edwards Deming na década de 1950, o modelo se inspira no trabalho de Walter Shewhart sobre controle estatístico da qualidade.
Sua lógica é simples: formular hipóteses, testar em pequena escala, medir o que mudou e institucionalizar o que funciona. Depois, recomeçar com um desafio um pouco mais ambicioso, criando uma espiral de melhoria sem fim.
Como estamos falando de um circuito fechado de melhorias, cada um desses ciclos se encerra com padronização ou correção e reinicia imediatamente, combinando ciência de dados, cultura de qualidade e disciplina operacional.
Confira: Excelência Operacional: como alcançar e manter padrões de qualidade excepcionais
Para que serve o PDCA e por que ele é tão usado?
Essa metodologia representa o alinhamento entre metas corporativas, processos operacionais e comportamento humano. Por conta disso, pode ser aplicado em inúmeros cenários, como:
- Reduzir variações em linhas de produção, call centers ou centros de distribuição;
- Acelerar a inovação ao testar hipóteses em pequenos lotes, diminuindo o tempo de lançamento de novos produtos;
- Promover cultura de dados, onde cada etapa exige métricas claras, o que incentiva a transparência;
- Sustentar certificações (ISO 9001, IATF 16949, GMP) ao criar trilhas de auditoria confiáveis.
No final, a força do método reside em três fatores: clareza (apenas quatro fases fáceis de lembrar), mensuração objetiva (toda decisão se ancora em dados) e cadência (ciclos curtos que mantém a equipe engajada).
Quais são as etapas do ciclo PDCA?
Agora vamos entrar nos detalhes sobre cada pilar dentro dessa metodologia.
P (Plan): planejamento
Nesta fase você define o problema, a meta e o plano de ataque, seguindo esses passos:
- Definição do problema: use dados históricos do MES ou ERP para quantificar o gap. Por exemplo: “taxa de retrabalho de 6% em abril contra meta de 2%”;
- Análise de causa‑raiz: combine ferramentas como Diagrama de Ishikawa, 5 Porquês e análise Pareto. Se o problema for complexo, aplique regressão múltipla ou ANOVA para isolar variáveis significativas;
- Meta SMART: específica, mensurável, atingível, relevante e temporal. Ex.: “Reduzir retrabalho para 3% até 30 de junho”;
- Hipóteses e contramedidas: documente o que acredita que vá resolver o problema: troca de fornecedor, ajuste de setup, treinamento, etc;
- Plano de ação: desdobre em tarefas com responsáveis, prazo, orçamento e KPI associado. Ferramentas como o 5W2H evitam lacunas.
D (Do): execução
Agora, é hora de colocar o plano em prática, mas de forma controlada.
- Escopo piloto: escolha uma linha, turno ou cliente para testar. Isso reduz risco e acelera o aprendizado;
- Padronização de coleta de dados: use checklists digitais para registrar variáveis de processo e evidências fotográficas. Assim, o “antes e depois” fica transparente;
- Treinamento rápido: micro‑learning de 15 min em linha, focado na nova instrução de trabalho. A curva de aprendizagem cai drasticamente;
- Monitoramento em tempo real: andons ou dashboards de IoT exibem OEE, tempos de ciclo e desvios logo que ocorrem.
C (Check): verificação
Em seguida, é hora de comparar o resultado real com a meta e avaliar se a hipótese se confirmou.
- Análise estatística: aplique teste t para duas amostras (antes × depois) ou carta de controle X‑barra. Se o p‑valor < 0,05, a melhoria é estatisticamente significativa;
- Revisão de indicadores secundários: verifique se não houve efeito colateral, como aumento de setup ou queda de segurança;
- Reunião de aprendizado: time multifuncional discute o que funcionou, o que falhou e o que surpreendeu.
A (Act): ação corretiva ou padronização
Pronto, por fim, é o momento de colocar tudo isso em prática:
- Padronizar: se a meta foi batida, atualize POPs, libere a nova versão no sistema de gestão documental e treine todo o turno;
- Corrigir: se ficou aquém, ajuste a hipótese ou escolha uma contramedida diferente e reinicie o ciclo;
- Escalonar: resultados positivos no piloto são estendidos para outras linhas ou filiais, sempre repetindo o PDCA localmente para absorver diferenças de contexto.
Como montar um ciclo PDCA eficiente, na prática?
O que fazer, então, para implementar essa metodologia?
Defina o problema com base em dados
Evite afirmações genéricas como “precisamos ser mais produtivos”. Use métricas objetivas: “OEE (Overall Equipment Effectiveness) de 68% versus benchmark de 80%”. Ferramentas de BI podem cruzar produção, manutenção e qualidade para revelar onde está a maior perda.
Estabeleça metas e indicadores
Conecte indicadores de processo a resultados financeiros. Por exemplo, cada ponto percentual de OEE equivale a 500 h‑máquina extras por ano, liberando capacidade que seria investida em novas máquinas.
Envolva a equipe operacional
Monte um time com operador, técnico de manutenção, engenheiro de processo e representante de qualidade. Diversidade de pontos de vista aumenta a acurácia da causa‑raiz e reduz resistência à mudança.
Use ferramentas visuais e checklists digitais
Substitua planilhas em papel por aplicativos mobile que geram QR Code para cada tarefa. Isso garante rastreabilidade, fotos em tempo real e dashboards automáticos.
Faça ajustes de forma iterativa
Prefira ciclos semanais a projetos de seis meses. Melhoria de 2% por semana resulta em ganho acumulado de 108% em um ano. Pequenos passos evitam paralisia por análise.
Qual a relação entre 5S e PDCA?
Antes de entender a relação entre essas duas metodologias, é importante saber o que é o 5S. Trata-se de uma prática originada no Japão que visa promover a organização, a limpeza e a padronização no ambiente de trabalho. O nome vem de cinco palavras japonesas que representam seus pilares:
- Seiri (Utilização): separar o necessário do desnecessário.
- Seiton (Ordenação): organizar os itens para fácil acesso e uso.
- Seiso (Limpeza): manter o ambiente limpo e seguro.
Seiketsu (Padronização): estabelecer normas e procedimentos para manter a organização. - Shitsuke (Disciplina): criar o hábito de seguir os padrões definidos.
Sendo assim, o 5S prepara o terreno para que o PDCA floresça:
- Elimina variações causadas por desorganização;
- Facilita a coleta de dados confiáveis, pois tudo tem lugar e identificação;
- Cria padrões visuais que se encaixam naturalmente no “Check” e no “Act”.
Quais são os benefícios do ciclo PDCA nas rotinas operacionais?
A aplicação do ciclo PDCA nas operações traz uma série de ganhos práticos e estratégicos para as empresas, especialmente em contextos que exigem alta eficiência, padronização e adaptação constante.
Um dos principais benefícios é a melhoria contínua. Ao promover ciclos de análise, ação e correção de forma sistemática, o PDCA mantém a operação em evolução constante, o que é essencial para se manter competitivo em mercados voláteis ou com forte regulação.
Outro impacto positivo é a redução de falhas. A etapa de checagem permite identificar desvios logo no início do processo, evitando perdas maiores, como a produção de lotes com defeitos ou a necessidade de recalls — medidas que comprometem custos e reputação da marca.
O PDCA também favorece a padronização de processos, criando uma base sólida para auditorias, como as da ISO 9001. Com documentação clara e atualizada, fica mais fácil manter a consistência das rotinas e acelerar o treinamento de novos colaboradores, reduzindo o tempo de adaptação.
Por fim, o ciclo estimula o engajamento da equipe. Ao envolver colaboradores na identificação de problemas e na construção de soluções, aumenta-se o senso de pertencimento e responsabilidade. Isso não só melhora o desempenho, como contribui para a retenção de talentos e a criação de uma cultura voltada para resultados.
Como a tecnologia pode apoiar a aplicação do PDCA?
A boa notícia é que sua empresa não precisa aplicar o ciclo PDCA de forma manual ou descentralizada. A tecnologia é uma grande aliada para garantir controle, padronização e agilidade em cada etapa do processo.
Por meio de aplicativos especializados, é possível digitalizar rotinas operacionais, acompanhar indicadores em tempo real e tomar decisões com base em dados confiáveis.
Aplicativos de checklist digital, ordem de serviço e monitoramento de processos
Com o Aplicativo de Checklist, sua equipe padroniza tarefas, coleta informações diretamente no campo e registra evidências com fotos, geolocalização e assinaturas digitais — tudo sem depender de papel. Já o Aplicativo de Ordem de Serviço permite comprovar a execução de atividades com mais agilidade, distribuindo tarefas automaticamente e garantindo o cumprimento dos prazos definidos no planejamento (Plan).
Além disso, a funcionalidade de monitoramento e dashboards embarcados ajuda gestores a executarem a etapa de verificação (Check) de forma prática, ajustando processos com base em evidências reais (Act). Com os dados certos na palma da mão, o ciclo PDCA se torna uma rotina viva e integrada à operação — e não apenas uma teoria no papel.
Acompanhamento em tempo real das etapas
IoT e SCADA alimentam painéis Power BI ou Grafana que mostram, minuto a minuto, se o processo está dentro do planejado. Alertas automáticos no Microsoft Teams ou Slack acionam times de resposta rápida.
Relatórios automatizados para verificação
Ferramentas de BI consolidam dados de múltiplas fontes, aplicam testes estatísticos e enviam alertas quando um KPI ultrapassa o limite superior de controle.
Registro de ações corretivas e padrões estabelecidos
Workflows de assinatura eletrônica asseguram que novos procedimentos entrem em vigor somente após validação gerencial, eliminando versões conflitantes de documentos.
Considerações sobre ciclo PDCA
Mais do que uma metodologia, o ciclo PDCA é uma forma de pensar e operar. Ele oferece um caminho estruturado, baseado em dados e centrado em pessoas, para transformar falhas e gargalos em oportunidades reais de melhoria.
Quando aplicado com consistência, ajuda empresas a crescerem com eficiência, reduzirem custos, padronizarem processos e manterem a equipe engajada — mesmo em ambientes complexos e competitivos.
Se, na sua operação, as melhorias ainda acontecem de forma pontual ou sem continuidade, talvez seja o momento de revisar essa abordagem. A cultura de melhoria contínua exige método, disciplina e ferramentas que sustentem essa evolução no dia a dia.
Quer entender como tornar isso possível com apoio da tecnologia?
Baixe nosso material gratuito dê o primeiro passo para estruturar sua gestão com mais eficiência.
Ou, se preferir, agende uma demonstração com nossos especialistas e veja como os aplicativos da umov.me podem apoiar a rotina das suas equipes — do planejamento à execução.
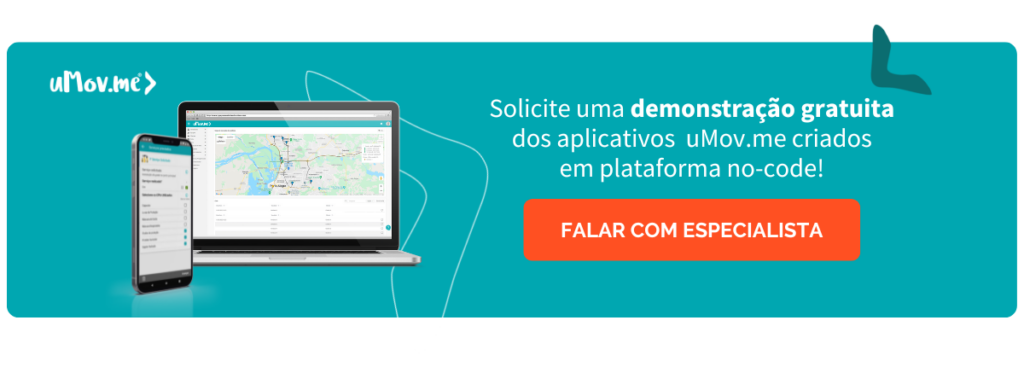